ZERO-POINT CLAMPING
ZERO-POINT CLAMPING TECHNOLOGY
Innovative zero point clamping systems for every application
STAY UP TO DATE
What we are doing
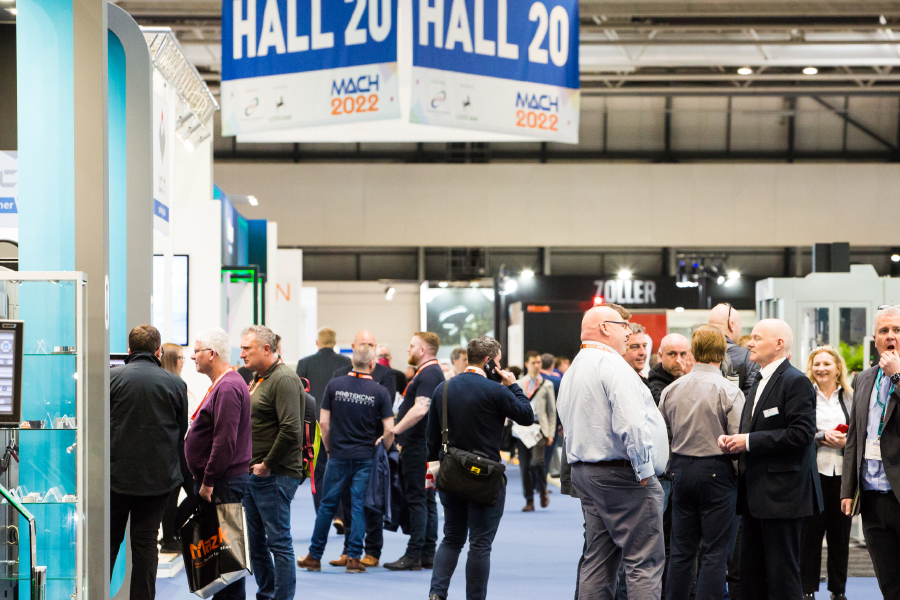
EVENT
MACH 2024
MACH is a fantastic event for both exhibitors and visitors. Showcasing live, digital production systems in one space, under one roof, hundreds
of millions of pounds worth of business is discussed, secured and completed at the event.
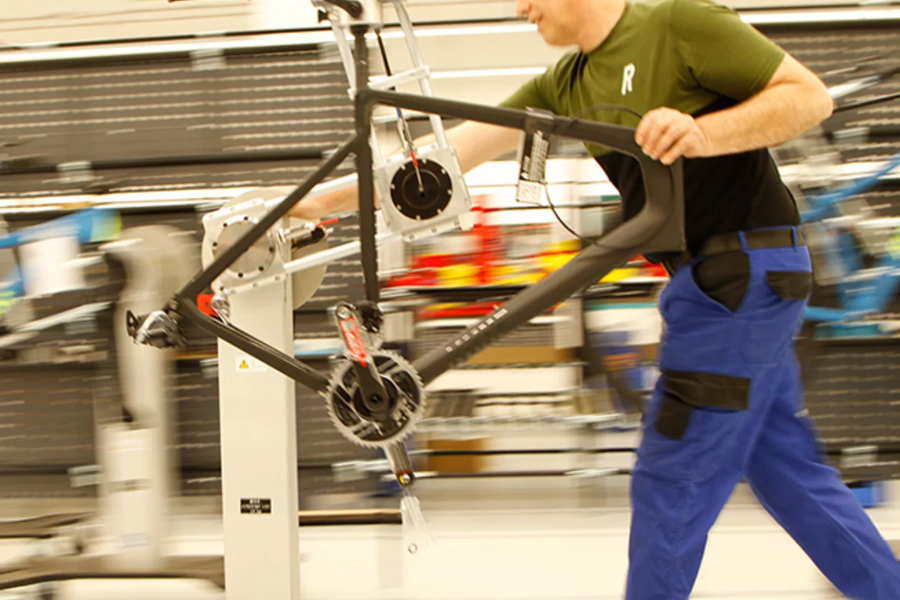
CASE STUDY
130 “Bike Promobil” facilitate work on every bike and in every position
How do you assemble 120 different bicycle and e-bike models weighing between 5 and 28 kg quickly and ergonomically? At ROSE Bikes in Bocholt the production is organised as a flow production with flexible assembly carts from ROEMHELD. They are the result of a joint development project. The variable assembly lines are highly productive and ergonomic; with a pleasant and stress-free working atmosphere, the bicycle manufacturer also attracts new employees.
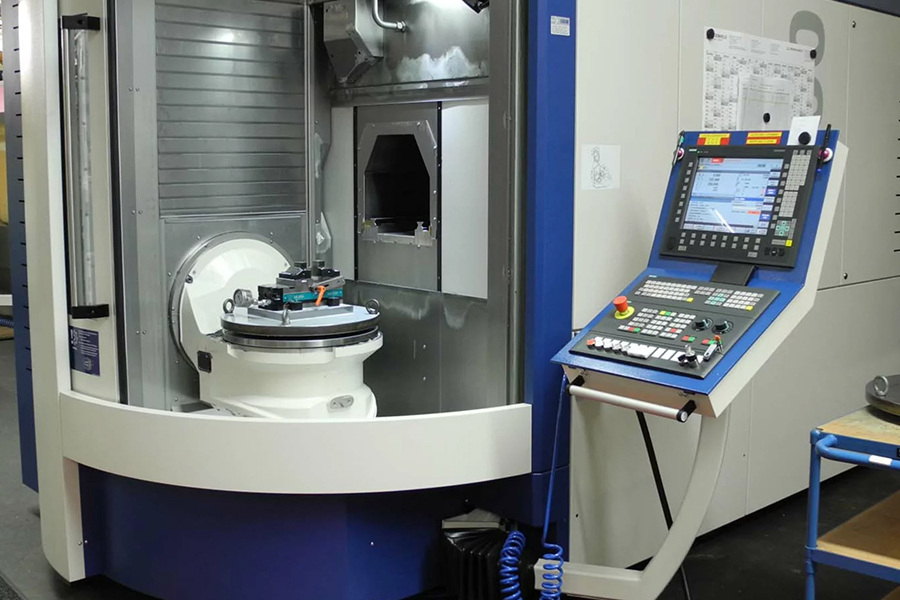
CASE STUDY
Constructive cooperation
If a manufacturer of workholding technology buys several 5-axes machining centres, these should certainly be equipped with their clamping elements and should be a reference for technically feasible solutions concerning effective set-up. The acquisition of three new Grob-Universal machines Series G350 and G550 by the Römheld GmbH required several changes – an effort that was worthwhile for both companies.